Construction Technology of Steel Belt Reinforced Spiral Corrugated Pipe
2024-06-20
Author:
Number of views:
Steel belt reinforced spiral corrugated pipeSpecial pipe fittings for hot melt belt during connection. Strengthen the connection strength and ensure the sealing effect. Ensure the reliability of system engineering. However, in actual construction, due to various man-made and non-man-made reasons, the construction effect cannot meet the ideal requirements, and even the pipeline interface is broken. Then, let's learn about it together.Steel belt reinforced spiral corrugated pipeConstruction technology!
Steel reinforced spiral corrugated pipe construction technology:
1. Connection mode Heat shrinkable tube connection
Steel belt reinforced spiral corrugated pipeIt is composed of reinforced fiber heat shrinkable material, hot melt adhesive and installation auxiliary material. The heat-shrinkable sleeve is located at the end of the two pipes to be connected, and the heat-shrinkable sleeve shrinks to make the two pipes into one. Features: safe and reliable, easy to install.
Steel belt reinforced spiral corrugated pipe connection structure: the heat shrinkable sleeve connection adopts fiber reinforced polyethylene heat shrinkable belt as the inner layer, the heat shrinkable tube as the outer layer, and the surface of the heat shrinkable tube is coated with hot melt adhesive. A method of connecting adjacent pipe surfaces to each other by tight hoop connections.
2. Construction steps of steel belt reinforced spiral corrugated pipe connection:
Steel belt reinforced spiral corrugated pipeThe construction environment temperature should be between -20 and 60. If the ambient temperature is lower than 0. Insulation measures should be taken; according to the process requirements of steel belt reinforced spiral corrugated pipe (gradually heated from the pipe connection to both ends), the following steps should be adopted for connection:
(1) Check whether the butt ends of the two connecting pipes are smooth. After the end faces at both ends are closed, the local clearance is less than 6mm. If the requirements are not met, on-site trimming is required until the requirements are met.
(2) Raise the ends of the two nozzles to keep a certain distance from the ground or trench wall (to facilitate the operation of heating tools around the park).
(3) Pierce the heat shrinkable sleeve at one end of the two connecting pipes and pull it to a position more than 500mm away from the connecting section (at this time, the protective paper layer on the inner wall of the heat shrinkable sleeve should not be damaged and should be complete. Prevent dirt, dust and water from entering the inner wall of the heat shrinkable sleeve).
(4) Grinding: The 120mm long cylindrical surface from the butt surface is rough, and the wave crest and valley shall be thickened with a wire brush, and at least three half-wave nodes shall be polished. The shape of the wire brush should conform to the shape of the corrugated pipe (each specification should match the wire brush).
(5) Clean the polished end of the tube with a clean cloth.
(6) Align and fix the two pairs of pipe sections without dislocation.
(7) In PE welding rod, a small beam of red flame or a small hot air beam sprayed from a small nozzle is used to heat the weld and welding rod, so that the welding rod is along the circumference (that is, the length of the weld is appropriate) to fix the joint of the two pipes.
(8) Preheat the circumference of the two pipe ends (two to three waves away from the butt end) with red flame to make the surface temperature reach 4050 (the preheating temperature should be 15 higher than the pipe ends) the softening point temperature of the hot melt adhesive. Available for surface thermometer monitoring.
(9) When the reinforced fiber heat shrinkable sleeve is wound and baked at the joint, it is required to wind at least one circle and make a firm circle.
(10) The surface temperature of the grinding line at both ends of the preheating zone can reach 4050. 10) The front belt at both ends of the grinding line is connected to make the surface temperature reach 40~50.
(11) Carefully move the heat shrinkable tube to one end of the grinding surface. The moving position is about: the distance from the initial heating point to the butt surface is about 13 times the length of the heat shrinkable tube (the length of each specification is determined according to actual experience), and remove the protective paper layer in the heat shrinkable tube (be careful not to stick dirt such as paper dust on the corrugated surface of the preheating steel belt and the pipe wall). In order to ensure that the circumferential gap between the heat shrinkable tube and the steel bellows is uniform, the other end of the heat shrinkable sleeve is supported by a wedge-shaped insulation made of anti-glue material, which is beneficial to improve the uniformity of shrinkage and the surface finish of the heat shrinkable tube.
RELATED INFORMATION
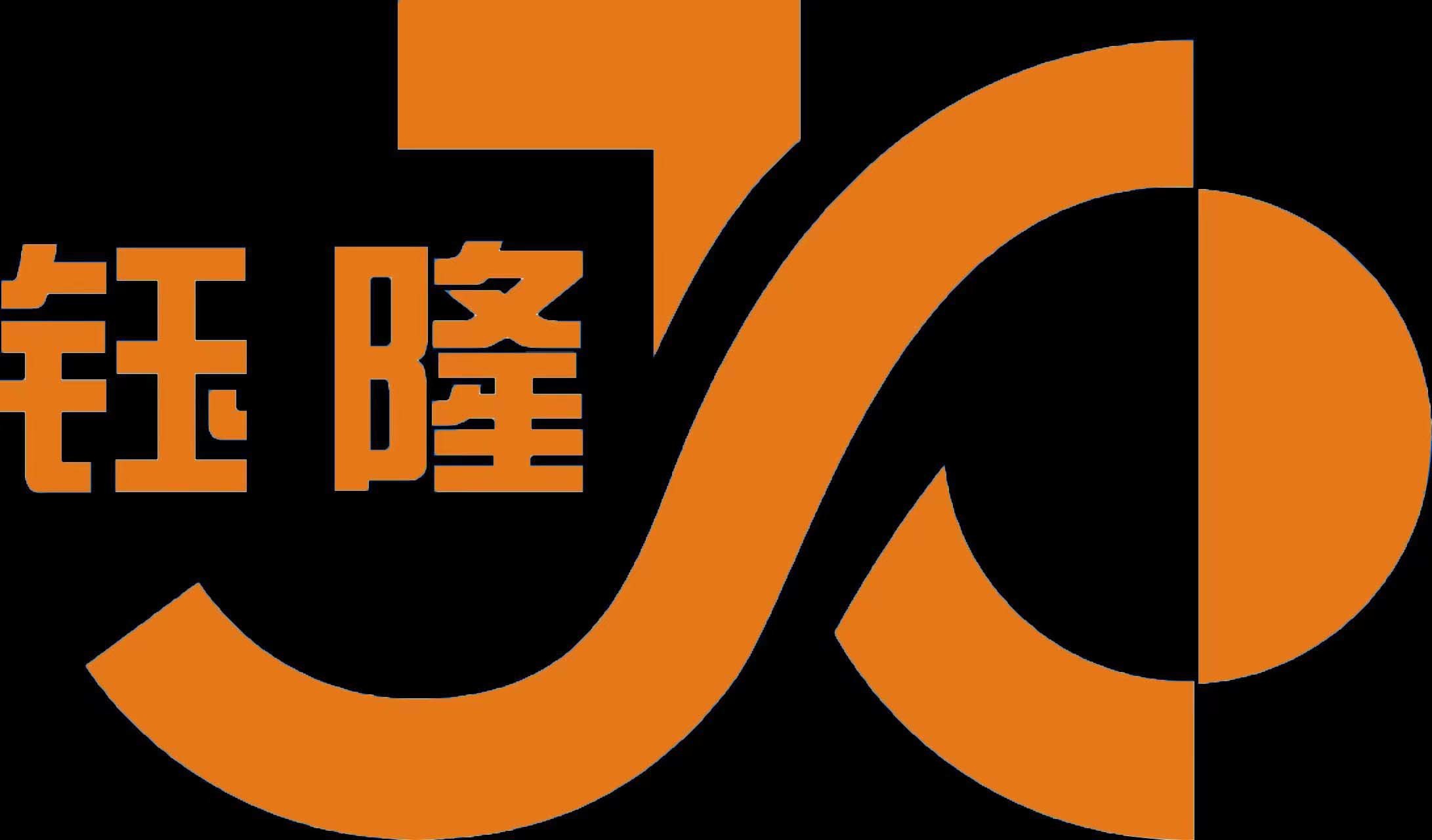
National customer service telephone
Site Map
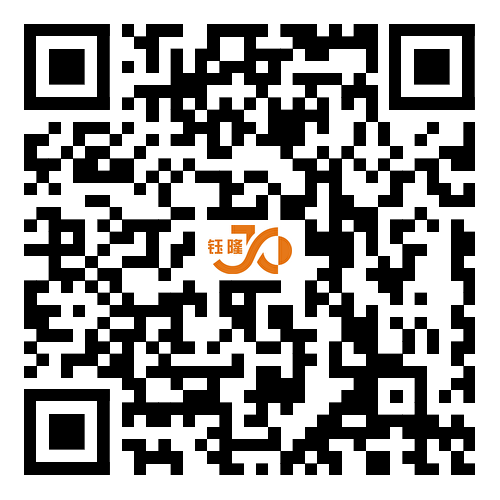
WeChat Public Number